DAIRY FACTORY AUTOMATION
ADDITIVE DOSING FOR THE DAIRY INDUSTRIES
ADos – Additive Dosing for the Dairy Industry
ULTRAVIOLET (UV) LIGHT TREATMENT IN THE DAIRY INDUSTRY
Ultraviolet (UV) light for the Dairy Industry
TANK PRESSURE CONTROL SYSTEM FOR THE DAIRY INDUSTRIES
Unipressure System – Tank Pressure control system for the Dairy Industry
CLEANING-IN-PLACE FOR THE DAIRY INDUSTRIES
CIP – Cleaning-in-place for the Dairy Industry
CARBONATION FOR DAIRIES
Carbonator – Carbonation for the Dairy Industry
MULTI COMPONENT MIXING FOR THE DAIRY INDUSTRIES
MultiMixer – Multi Component Mixing for the Dairy Industry
FLASH PASTEURIZATION FOR THE DAIRY INDUSTRIES
FlashPasto – Flash Pasteurization for the Dairy Industry
WATER PRE-TREATMENT FOR THE DAIRY INDUSTRIES
Water Pre-Treatment for the Dairy Industry
WATER PRE-TREATMENT
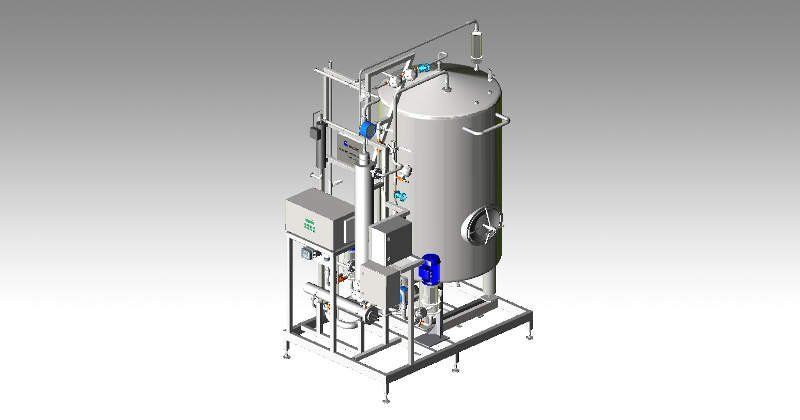
Sand & Multi Media Filter
A sand filter only uses sand as filter medium. Whereas a multi media filter typically have 3 to 5 layers of different media types. Both are back-flushable. In a sand filter the smallest particles are trapped at the top of the media bed, while larger ones sink deeper proportional to their mass. The result is a very limited use of the media depth, because virtually all filterable particles are trapped at the very top of the filter bed. Multi media filters use several layers of different materials, each having a significantly different density. Due to the layering, larger particles are removed first at the top of the media bed, while smaller particles are trapped further below. Trapping particles in this manner, results in more effective removal of contaminants, even of very small turbidity forming particles. Furthermore, longer run times between backwash cycles are achieved.
De-Ironizer
Dissolved iron and manganese are removed from water by oxidation and subsequent filtration. Fe2+ is oxidized to Fe3+, which with oxygen, forms the insoluble iron complex Fe(OH)3. Mn2+ is oxidized to Mn4+, which with oxygen, forms insoluble MnO2. An ideal and low-cost method of providing oxidation is to use the oxygen in air as the oxidizing agent. For removal of the insoluble iron and manganese gravel can serve as filtration media. By cyclical back-flushing the iron and manganese particles are washed out and removed.
Activated Carbon Filter
Activated carbon filtration is a method of filtering that uses a bed of activated carbon to remove contaminants by chemical absorption. Due to the highly porous structure of activated carbon, each carbon particle provides an extremely large surface area. Contaminant molecules are trapped inside this structure. Activated carbon adsorbs organic substances which cause odours and tastes. Furthermore, it acts as a catalyst in contact with free chlorine supporting the reaction of free chlorine to harmless chloride ions.
Disinfection
Chlorine is an inexpensive treatment method for deactivating microorganisms like bacteria and viruses. Stored in pressurized containers, it can be injected as a gas directly into the water. Alternatively, a sodium hypochlorite solution can be used. This solution is easier to handle than chlorine gas. Disinfection can also be achieved with calcium hypochlorite, a solid disinfectant. This form can be stored as powders, granules or tablets. Ozone (O3) is another powerful oxidizing agent. It is pumped into water systems to kill biological contaminants like bacteria and viruses. Since ozone gas is very unstable, O3 needs to be created on site. Ozone is pure active oxygen and produces no residual odours or tastes in water. Also ultraviolet (UV) light can be used to kill harmful microorganisms. The UV process is an attractive option in many cases because it is chemical-free and investment costs are low.