Turning up the pressure for consumer product safety
The highest priority in the production of food, beverages and pharmaceuticals is product safety. In sanitary applications, such as the production of vaccines or baby food, the purity, quality and stability of the product must be ensured.
Critical, sanitary and sterile applications such as the food and beverage , dairy, breweryand life sciences industries demand hygienic design. A crucial element in these markets is the ability to indicate the pressure in manufacturing pipelines, fermenters or manufacturing facilities via easy-to-read pressure gauges. In addition, pressures and vacuums must be monitored constantly during cleaning, sterilisation and testing. This process reliability can be guaranteed by making the correct choice of hygienic pressure transmitter; ensuring you get accurate, repeatable results with no maintenance over extended periods.
Robust, needs-based, cost-effective
INSTEK Control cc,
in conjunction with Anderson-Negele, offer our clients in sub-Saharan Africa an extensive range of sensors to make all fluid processing application efficient and reliable. Anderson-Negele’s new P41 temperature compensated pressure transmitter is robust, needs-based and cost-effective.
For many standard applications, a sensor which precisely measures the pressure and reliably transmits it to the PLC, is perfectly sufficient. The new P41 is an inexpensive, compact, temperature-compensated pressure sensor that offers the right solution for applications.
The P41 is designed to meet high process requirements, offering pressure ranges up to 40 bar, overpressure resistance up to 100 bar, and vacuum resistance. The measuring range can be individually adapted to the desired process pressures and a choice can be made between absolute and relative measuring cells. Compound measurement is also possible, which means the relative measuring cell can be used to measure the vacuum range. The P41 is also robust when it comes to temperatures: up to 125 °C as standard, up to 150 °C / 60 min for CIP/SIP cleaning, and even up to 250 °C permanently with optional cooling section. The entire sensor, including the diaphragm, is made of stainless steel for excellent cleanability and durability.
Pressure sensors for level measurement: the right measuring method for every application
The pressure transmitter P41 completes our Anderson-Negele product range of pressure and limit sensors: D3, L3, LAR, DAN-HH and P41. The P41 is also very variable in terms of process connections and offers, in addition to the hygienic thread "G1" with CLEANadapt, further connections according to DIN 3852 in "G1/2" and "G1", Tri-Clamp and Varivent. With this comprehensive range of sensors based on different measuring methods, you can always find a measuring instrument for process pressure and level measurement that is precisely tailored to your application.
The complete process sensor system from a single source
INSTEK Control ccprovide our clients with a wide range of Anderson-Negele sensors to make all fluid processing applications safer and more efficient. For temperature, pressure, filling level, limit level, flow rate, conductivity and turbidity, the measuring methods are adapted to the special requirements of your industry.
Contact us
to discuss your hygienically designed process.
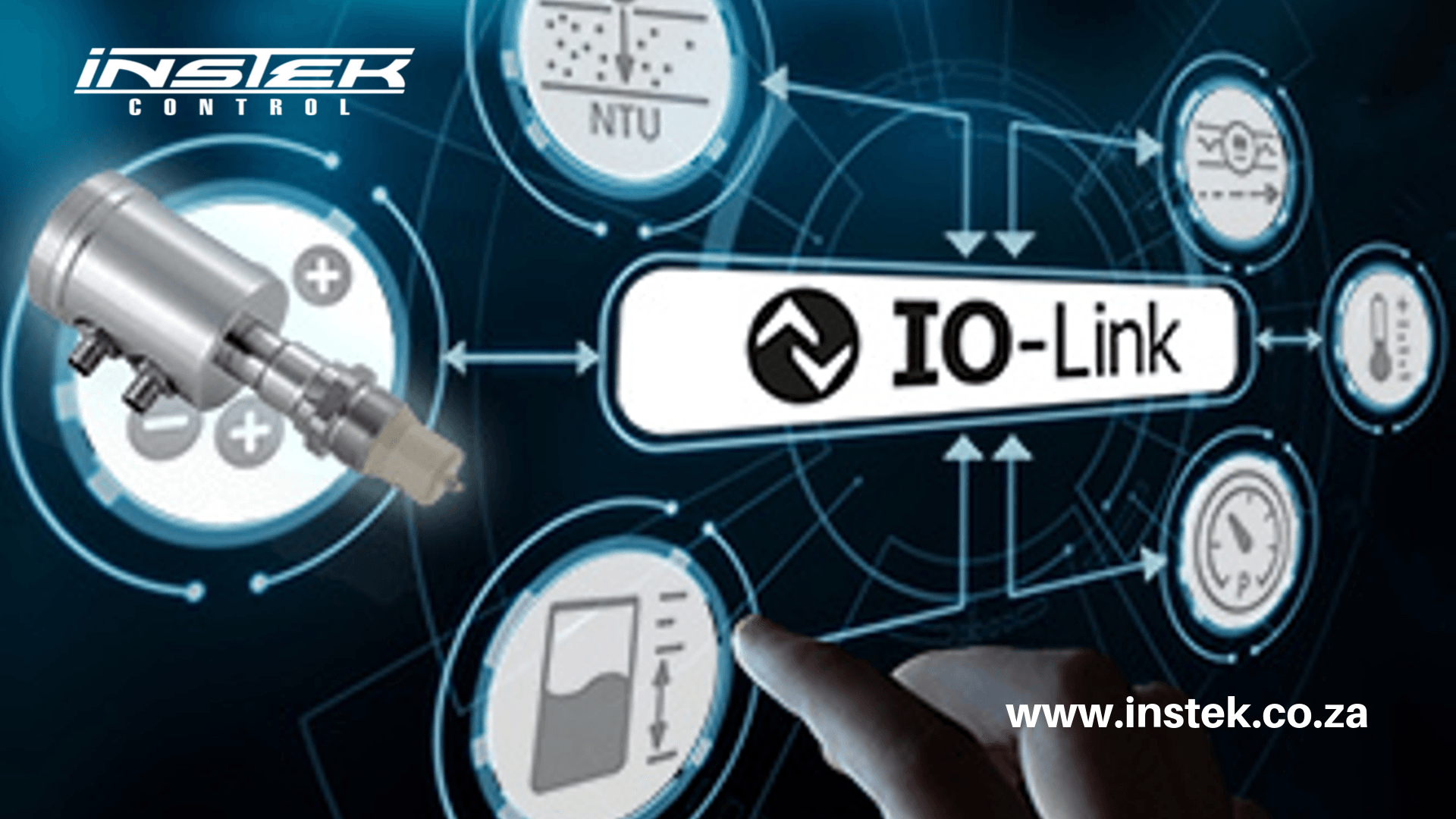
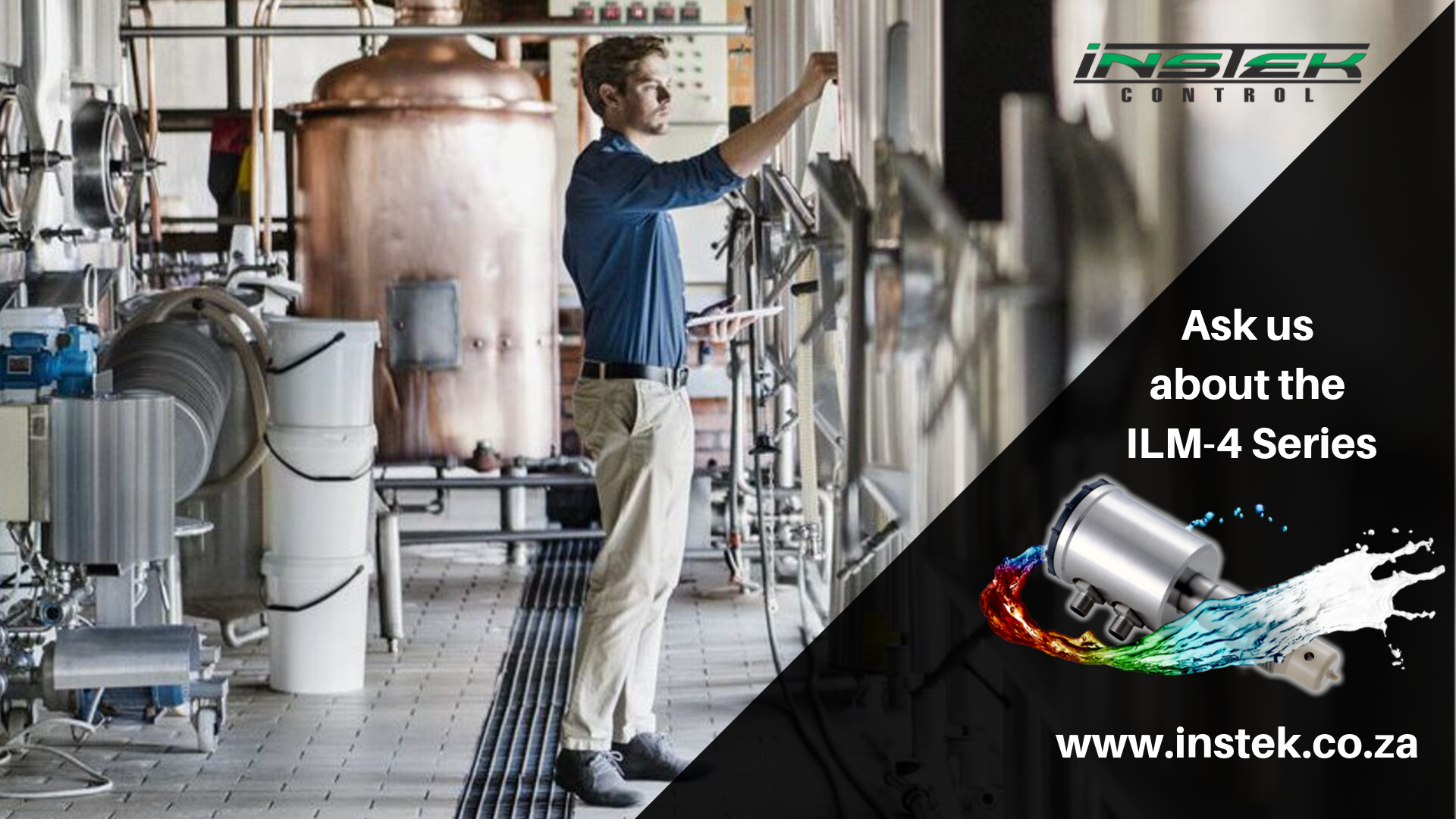