Alternative to traditional measurement systems
LTM-2 level measurement probes from Instek Control cc are aimed as being an alternative to traditional measurement systems still employed throughout the flotation industry.
Designed and developed in Germany, the LTM-2 probe was specifically made to meet flotation challenges in the industry. This probe is a two-wired loop and is made from high grade stainless steel. With no moving parts and using the Electro Potentiometric Effecta, a patented form of conductivity it is able to determine pulp/froth interface.
Booysendal Platinum’s concentrator plant in 2016 agreed to prelimenary trials on a unit supplied by Instek Control's distributor in the Mpumalanga and Linpopo area, Redland Engineering cc. The LTM-2 probe was trialed on a column float cell, a cleaner float cell and on a concentrate sump , all applications known to pose difficulties IRO accurate level measurement when utilising conventional measurement methods.
Prior to these trials, level measurements were achieved by means of a bubbler for these columns, a ball-and-striker plate for the cleaner float cells and an ultrasonic level sensor on the concentrate sumps. All methods posed challenges, which can result in production losses, i.e.
Bubbler’s on Column Floatation:
- Variations in air supply to the bubbler tube affected the bubbler level readings
- Bubbler level readings are sensitive to density changes in froth and pulp phases
- Frequent chokes occur on bubbler tubes
- Calibration on bubbler tubes is labour intensive and needs to be carried out on a regular bases
- False level readings cause instability to down-stream processes as well as unnecessary wear on control valves
Float Balls, Striker plates and Ultrasonics on Floatation Cells
- Losses occur due to either the ball and striker plate “getting stuck” or when the float ball detaches itself from the rod.
Ultrasonics on Concentrate Sumps
- Froth buildup in the concentrate sumps results in false high level readings which in turn reduces the masspull in the float cells feeding into them (Floatstar controls the air on the float cells according to the level reading from the concentrate sump). The reduced masspull decreases the level in the sump whereby this scenario creates even more froth and the net result is production losses due to low masspulls and unstable operation due to concentrate pumps cavitating.
The LTM-2 probe had the following advantages when installed in place of the ultrasonics:
- No moving parts
- Not density dependent
- Not sensitive to froth or product build-up
- Set up can be achieved in less than 5 minutes
- The LTM probes are Virtually maintenance free
- The unit accurately measures the pulp/ froth interface and provides a stable feedback signal at an optimal update rate, without excessive “damping” all of which provides improved process control and stability
Booysendal Platinum subsequently have replaced all bubbler tubes with LTM-2 probes and will consider phasing in LTM-2 probes in the concentrate sumps on the cleaner circuit and with a view to implement them in the flotation cells in the future.
The following trends and observations were provided by Booysendal Platinum to indicate the advantages of the LTM-2 probe compared to the conventional level detection systems.
For more information, contact Raymond Karsten,
Instek Control +27 (0) 12 998 6326 | 0861 INSTEK (467835)
www.instekcontrol .com | www.ltm-2.com
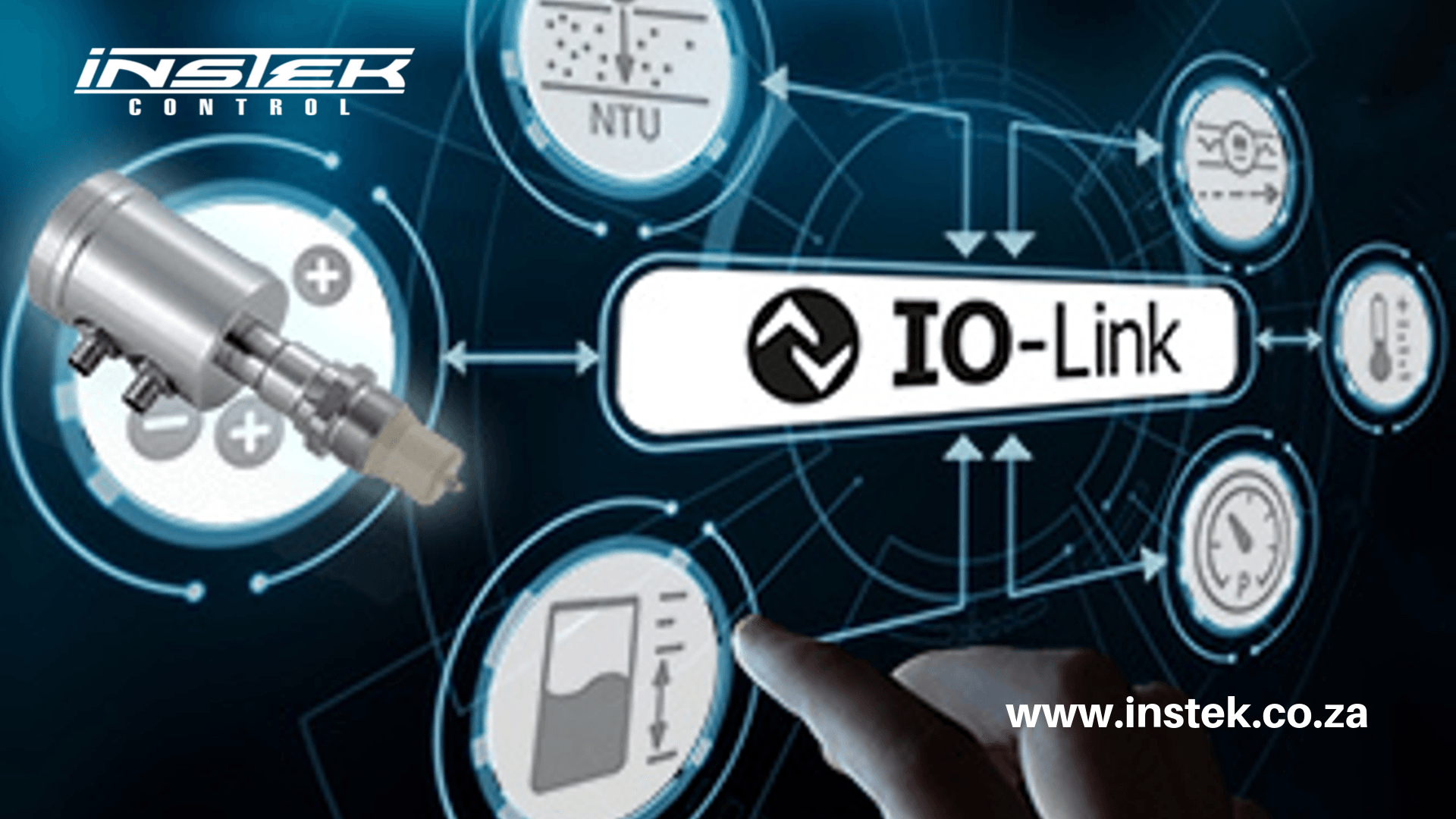
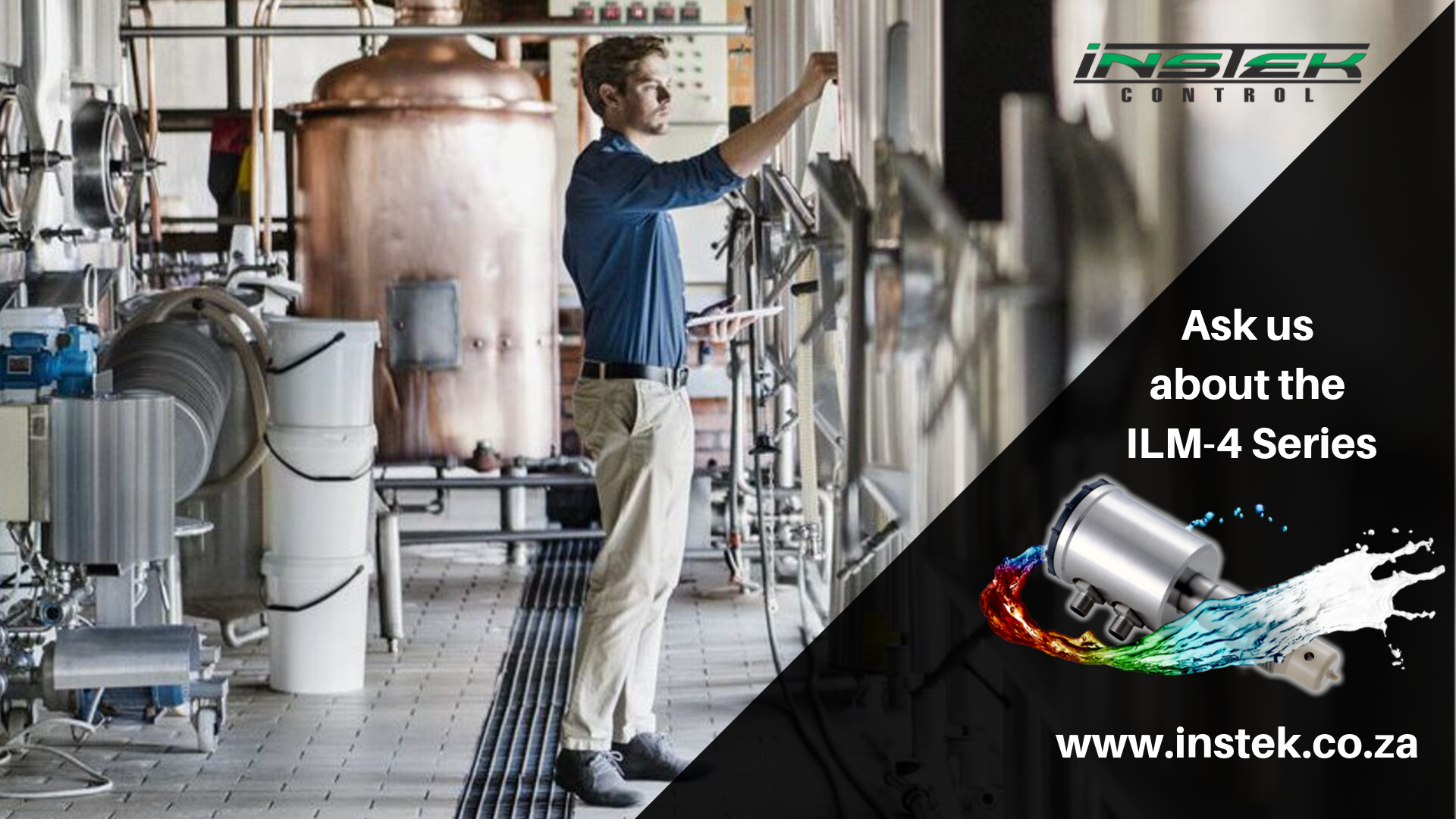