Simple, straight forward and tremendously effective
Without any doubt the best mixing system for carbonation and mixing of liquids and gasses to date - Venturi Vortex Injector by Centec GmbH.
Giovanni Battista Venturi “discovered” the venturi effect in 1797, and ever since the Venturi effect have been in use in fluid and airflow mechanics over a range of disciplines ranging from Aeronautics to Farming, and everything in-between.
For the Food and Beverage Industry, Centec GmbH developed the Vortex Injector using the same principle to create arguably the best mixing system for carbonation and mixing of liquids to date.
The working principle is straight forward. Fluid moves through the inlet chamber where it is accelerated and pressurized.
Moving through the mixing chamber there is an immediate pressure drop that opens the liquid and creates a vacuum. This creates conditions for a near perfect fusion of liquids and or gases. The gas or liquid is injected into the product through multiple nozzles around the circumference of the mixing chamber. The homogenous mixing of the products take place instantaneously.
The Centec Vortex Injector is especially designed for the homogeneous mixing of liquids and Gas, e.g. CO2, O2 or N2, with beer, wine, or other beverages.
Because this system is so effective the dissolving times are greatly reduced and the dosing can be done precisely and accurately. It is a proven system implemented in major Breweries, Wineries, and Soft Drink concerns.
The Centec Vortex mixer is a hydrodynamic fitting for the mixing and dispersion of multiple liquids and further applications include additive dosing of liquid ingredients (e.g. flavors, sweeteners, vitamins, colors) to a main stream.
The benefits of the Venturi Vortex Injector are numerous and includes:
·Instant, homogenous Mixing and additive dosing of liquids and gasses.
·Designed for each specific application with the unique characteristics of each product and process incorporated.
·Full CIP Capability
·Outstanding Price-to-Performance ratio
·Smaller holding loops and dissolving times resulting in more compact plant designs
·More accurate dosing ability resulting in material and time savings.
For more information visit VORTEX or contact Raymond +27 12 998 6326 / raymond@instek.co.za.
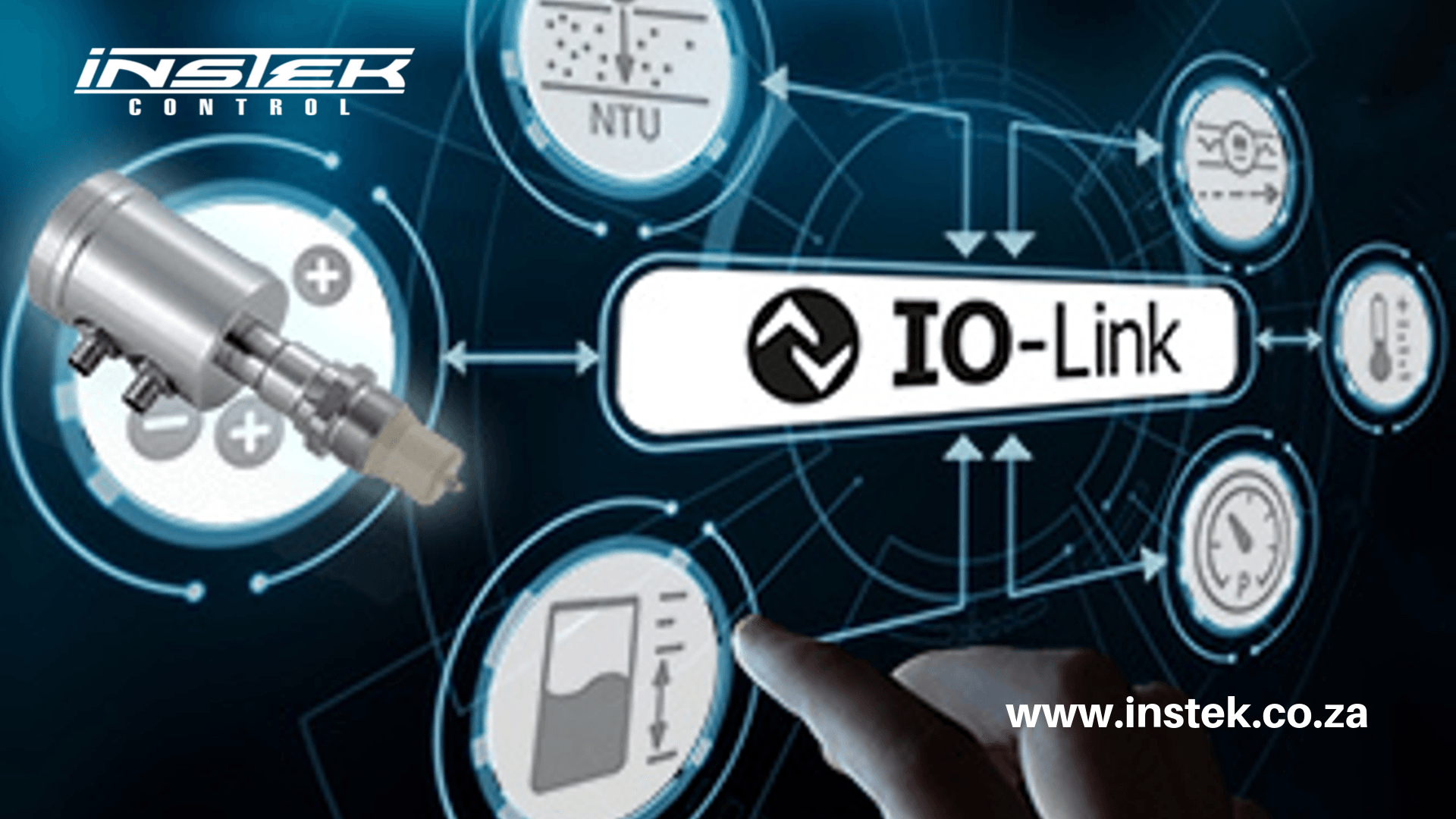
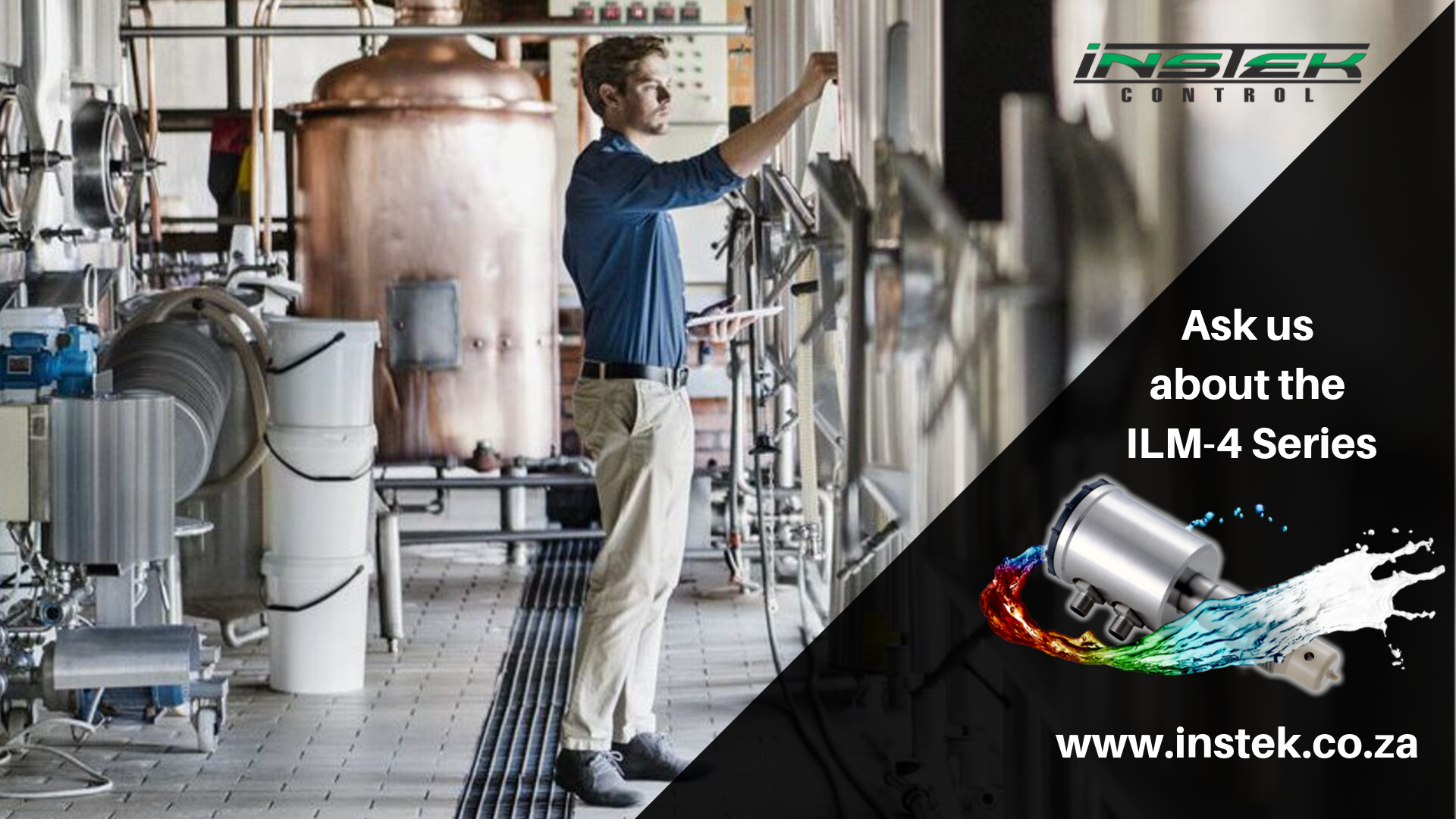