Application cases - SOFT DRINK PRODUCTION - solution for Biofilm....
Bacterial growth on surfaces in contact with water and other liquids (a phenomenon usually known as “biofilm” or “bacterial slime”) causes many issues in Food and Beverage Production. Indeed, such bacterial layer is the ideal environment for the proliferation of pathogens. Moreover, biofilm is much more resistant to sanitation that free-floating bacteria, and this resistance increases with time.
In this soft drink production plant, Clean-In-Place(CIP) was applied on a scheduled time-basis. To verify the real effectiveness if CIP treatment against biofilm, the Customer decide to install an ALVIM sensor in the feed water line of the beverage production plant. The following data illustrate the most relevant results of the biofilm monitoring that was carried out in this industry over several months.
As it can be seen in Figure 1, the Alvim Sensor detected biofilm growth about 10 days after the installation in the soft drink production plant. Since the Alvim Technology detects biofilm growth from its very early phase (first layer of bacteria), the scheduled CIP treatment, that was applied a couple days after bacterial growth, easily removed biofilm.
After some weeks, the Alvim probe detected biofilm growth again (Fig.2). Also in this case the scheduled CIP treatment was applied a couple days after bacterial growth and, again, the cleaning treatment completely removed biofilm.
The ALVIM Sensor demonstrated that the application of CIP was timely enough, during the considered period, even if a small adjustment (anticipating the treatment of 4-5 days) would have prevented bacterial growth inside pipelines even better.
The indication provided by the Alvim Biofilm Monitoring System
allowed to check, on line and in real time, the actual need of a cleaning
treatment, and the effectiveness of CIP.
If you have a similar problem with Biofilm, contact Instek Control for more information on this incredible sensor. info@instek.co.za or 012 998 6326
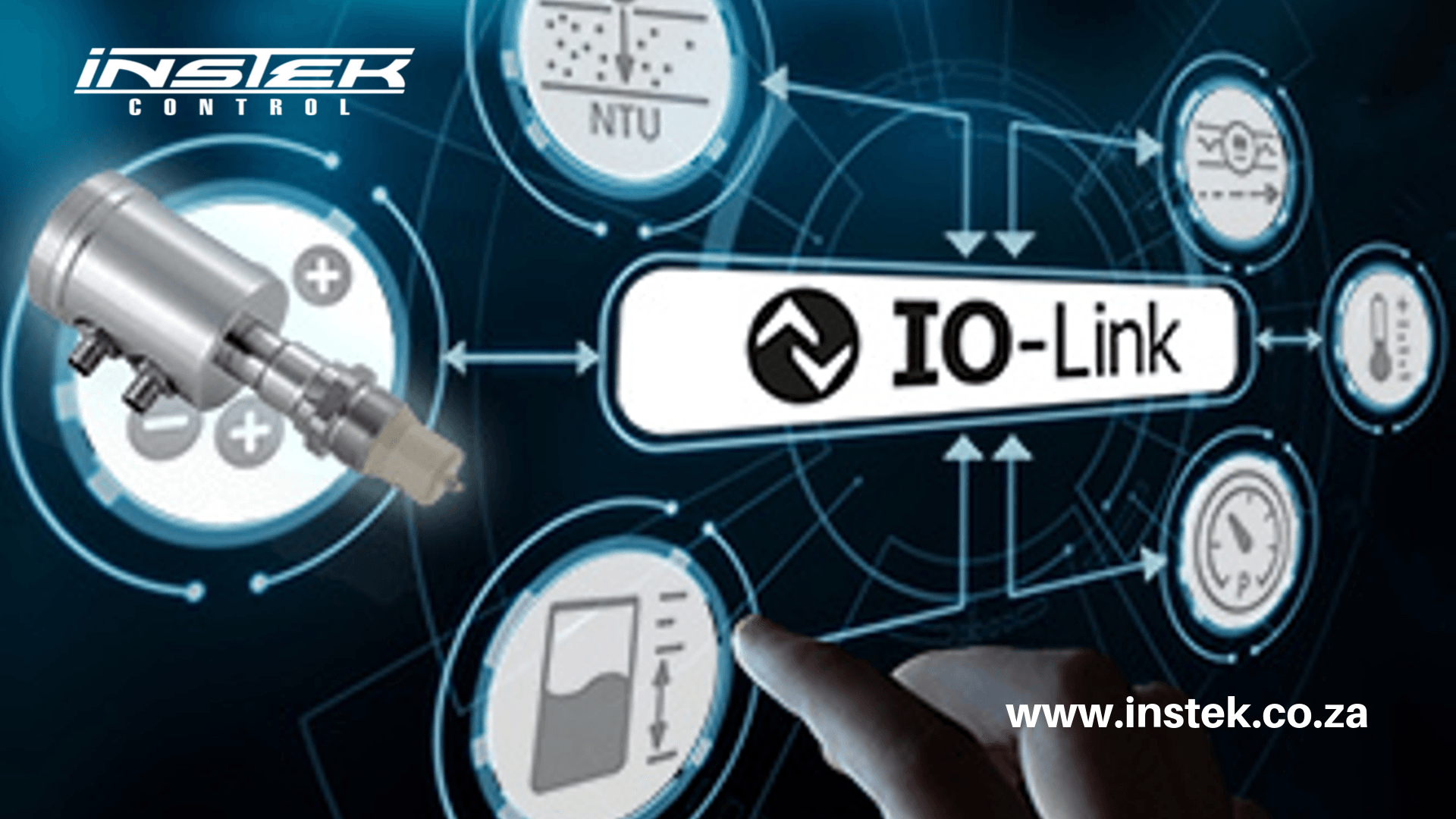
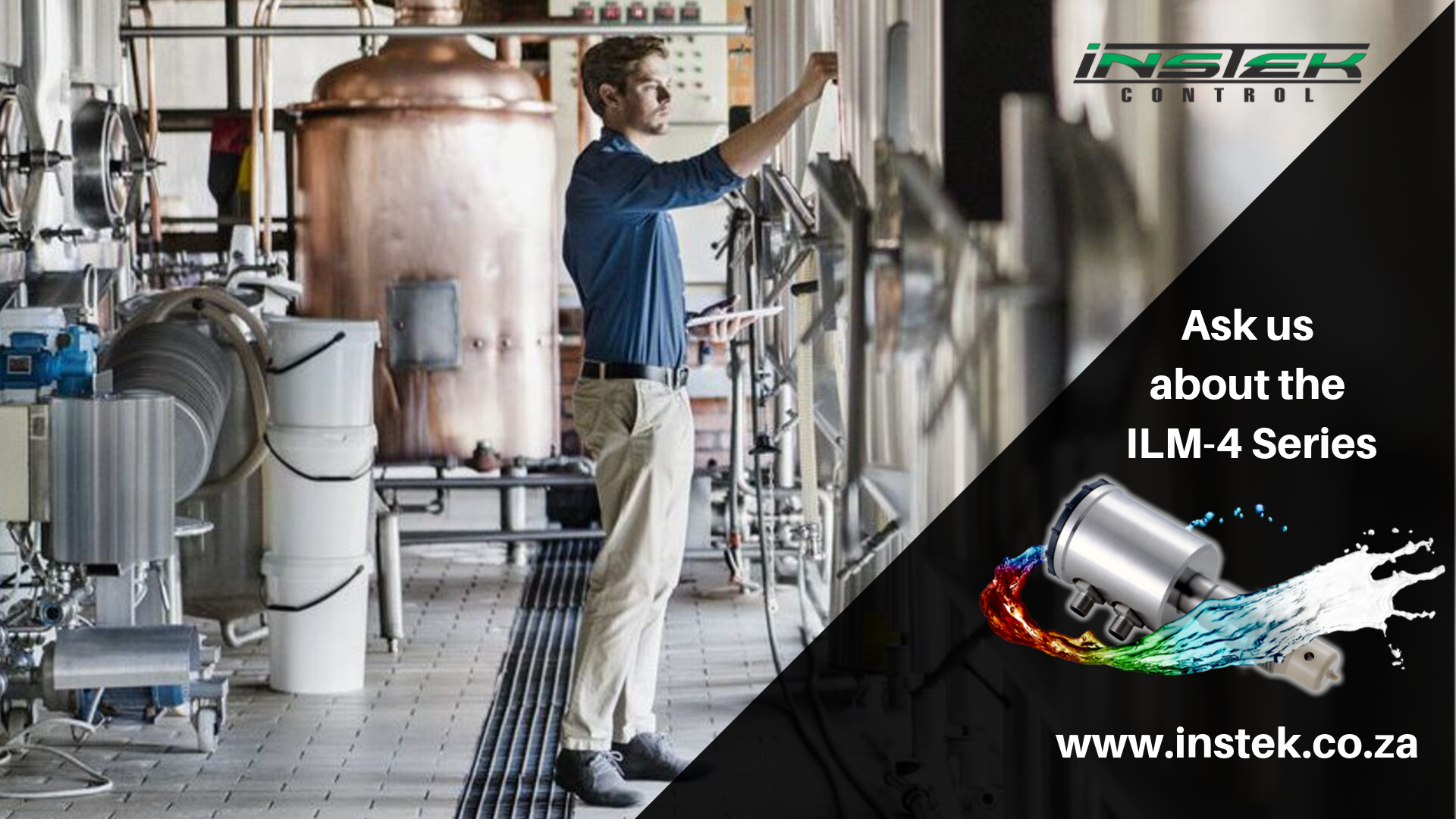