Clean-In-Place (CIP) check and optimization made easy
Without an online, real-time bacteria detection device, able to monitor microbiological growth since its first phases, it is difficult to check if Clean-In-Place is really effective, or if it needs to be adjusted.
To limit bacterial growth on the internal surfaces of pipes and tanks (a phenomenon usually known as "biofilm" or "bacterial slime"), most industries apply Clean-In-Place (CIP). Such treatment entails the injection of chemicals in the process line, to remove both deposit (organic and inorganic fouling) and microorganisms (biofilm). Different formulations and approaches exist (acid+basic, monophase, enzymatic+disinfectant, etc.), and also timing/schedule greatly differ among different applications. Most often, CIP is applied on a fixed time-basis, without any check on the real need or efficacy. Unfortunately, being microbiological growth a dynamic phenomenon, influenced by plenty of variables, a "one for all seasons" cleaning strategy does not exist. For this reason, a check on CIP real effectiveness is needed, to avoid microbiological issues like proliferation of pathogens, microbial corrosion and others.
ALVIM Biofilm Probeshelp to detect and monitor bacterial settlement and growth inside water lines, tanks, and other surfaces in contact with the water and other liquids allowing to check, at the same time, the efficacy of CIP, sanitation and biocide treatments.
The ALVIM Biofilm Monitoring System has been already used to check and optimize Clean-In-Place treatments in:
Standard laboratory analyses (culturing techniques / plate count / HPC) have many limitations, since they are:
- time-consuming, they usually require 24 - 72 hours;
- poorly representative of the real abundance of bacteria, since less than 1% of the bacteria present in a sample will grow in lab conditions;
- applied to water samples, but most bacteria live in biofilm, not free in the water. It is well known that the two phenomena are mostly unrelated: after the settlement of the first free-floating bacteria coming from the water bulk, biofilm dynamics are almost completely unrelated to the presence/number of bacteria in the water, since the settled ones will grow exponentially, duplicating themselves.
Bacteria detection kits are receiving a growing interest, since they provide a first screening in a short time. Unfortunately, the results provided by such kits are not always representative of the actual presence and abundance of bacteria in the piping system, e.g. if they are applied to water samples, as explained above. Moreover, bacteria detection kits provide a "spot" measurement, not an online, continuous indication of bacterial growth.
For more info, visit the ALVIM Biofilm Sensors page
, or contact Instek Control 012 998 6326 / info@instek.co.za
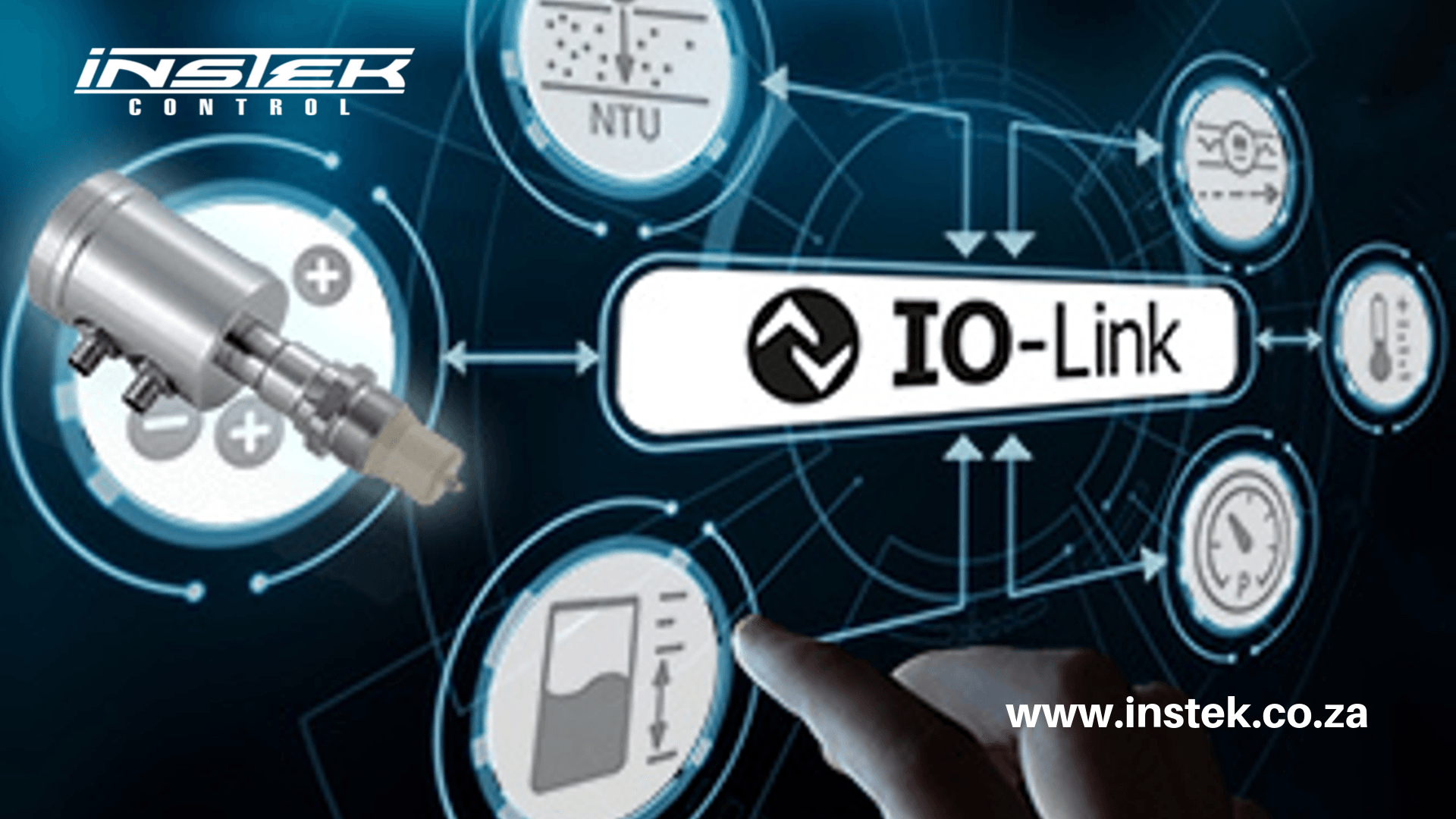
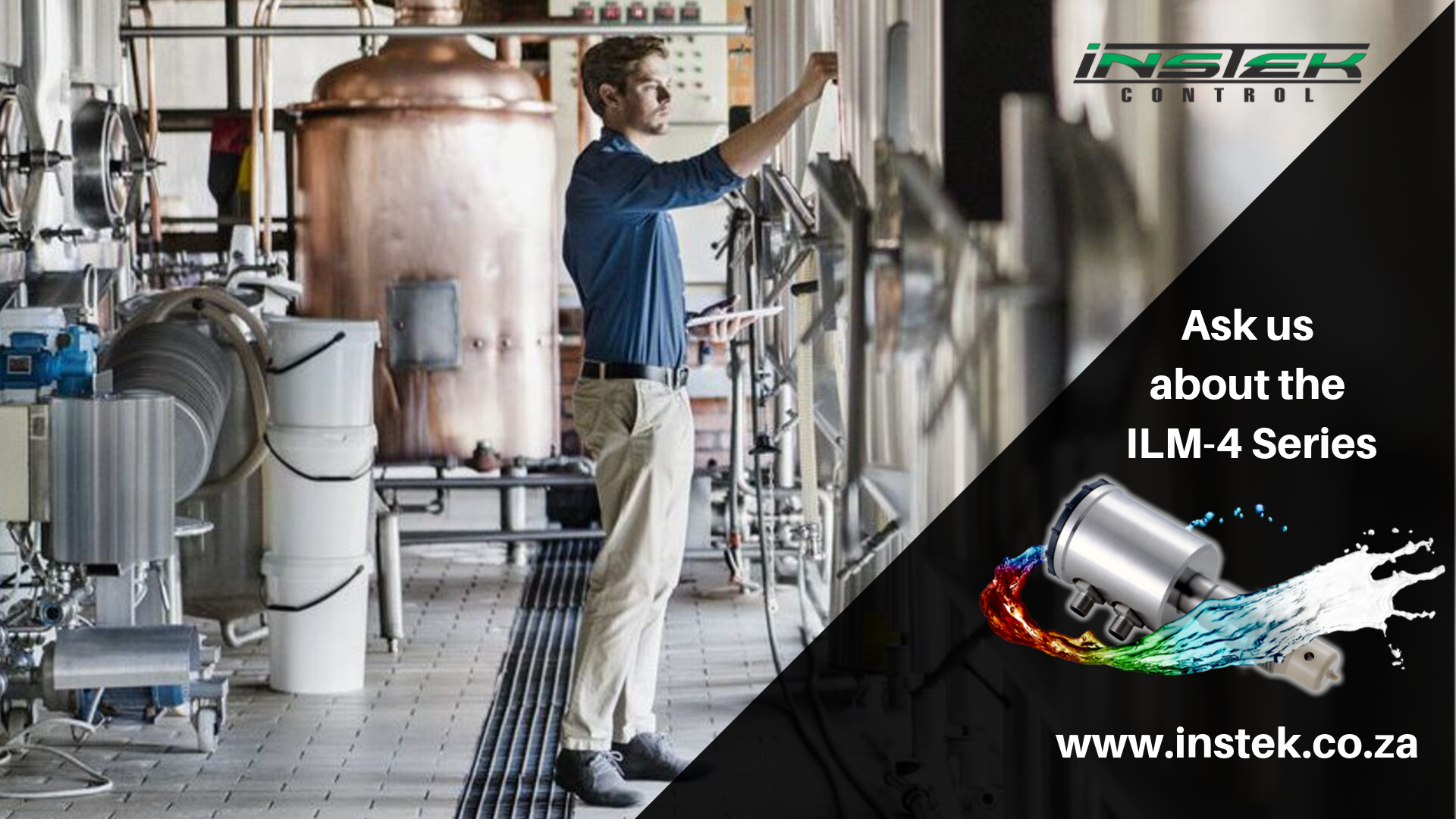