DeAlco Tec – Dealcoholization of beer
The dealcoholization system DeAlcoTec applies an aroma conserving method to remove alcohol from beer after complete fermentation. Ingredients are conserved to a particularly high degree or added back to the beer. The dealcoholization temperature is low and it is possible and the residual alcohol content is close to the detection level.
For dealcoholization incoming alcohol rich product is first gently heated by a regenerative heat exchanger in counter current to the finished product. It is dispersed at the top of a specially designed evaporation column. For CO2 containing product, prior degassing prevents formation of foam. Exhaust vapours are fed into the bottom of the column. They rise upwards inside the column in counter current to the falling warm liquid. Thereby, they remove the volatile alcohol from the product. The less volatile components fall to the column base. They flow into the falling film evaporator that generates the exhaust vapour for delacoholization. Densely packed, thin stainless steel sheets in the column maximize the transfer surface and the contact time between the product and the exhaust vapours. The complete process takes place under vacuum. A key benefit of the Centec technology is the exceptionally effective alcohol removal at low temperature. The remaining alcohol-free product is pumped away and cooled for storage or further processing, e. g. for carbonation. The volatile flavours from the original product can be separated from the exhaust vapours in a special aroma recovery system and added back to enhance the taste of the finished product. If desired, the alcohol is concentrated to form liquid alcohol of up to 90 vol. % for use in other applications or for sale.
For highly precise measurement and control of critical product characteristics such as alcohol, O2 and CO2 content, Centec process sensors are ideally suited. Centec have decades of experience in the development and manufacturing of own precision instruments.
Contact Instek Control today for more information: info@instek.co.za
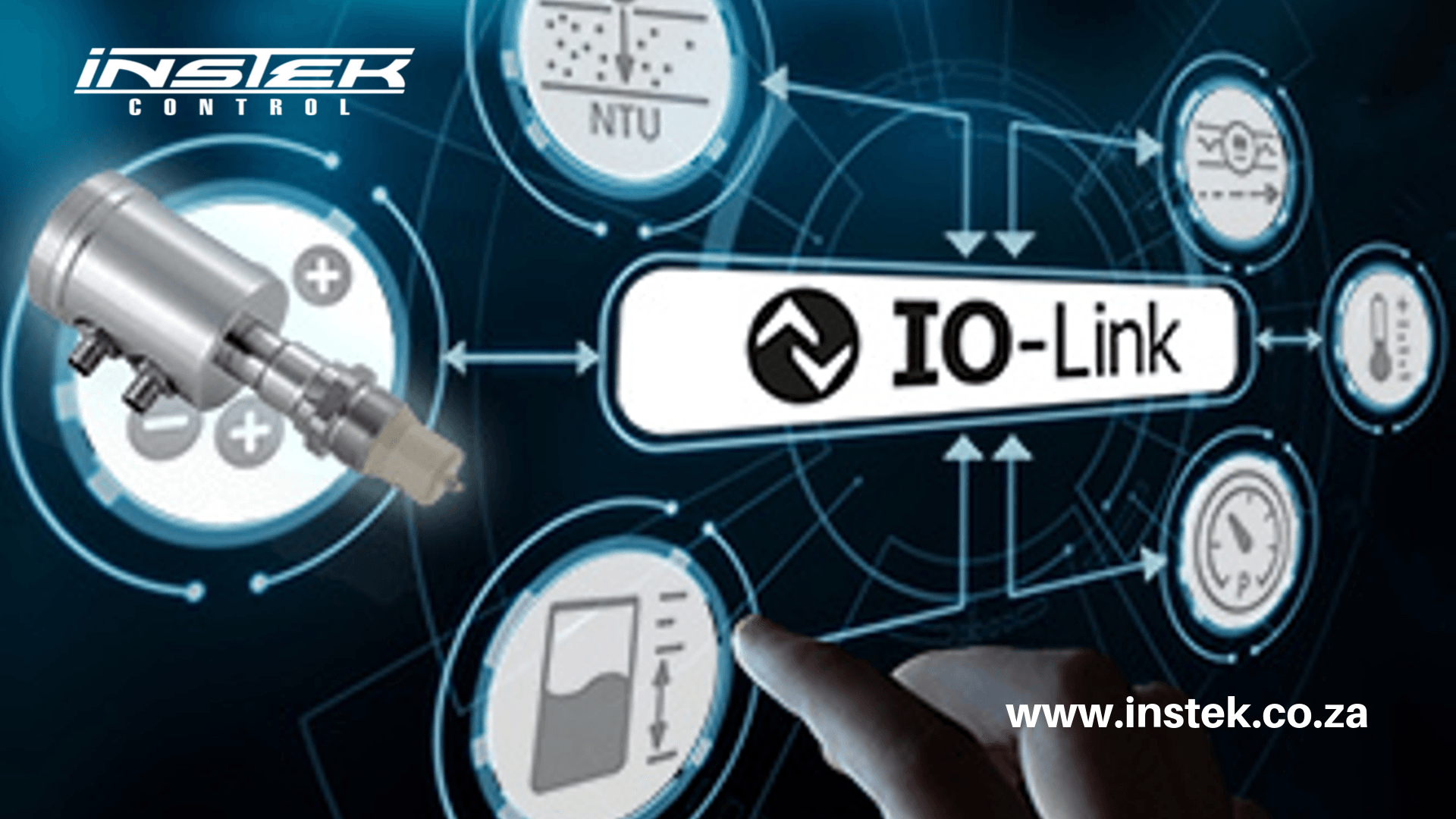
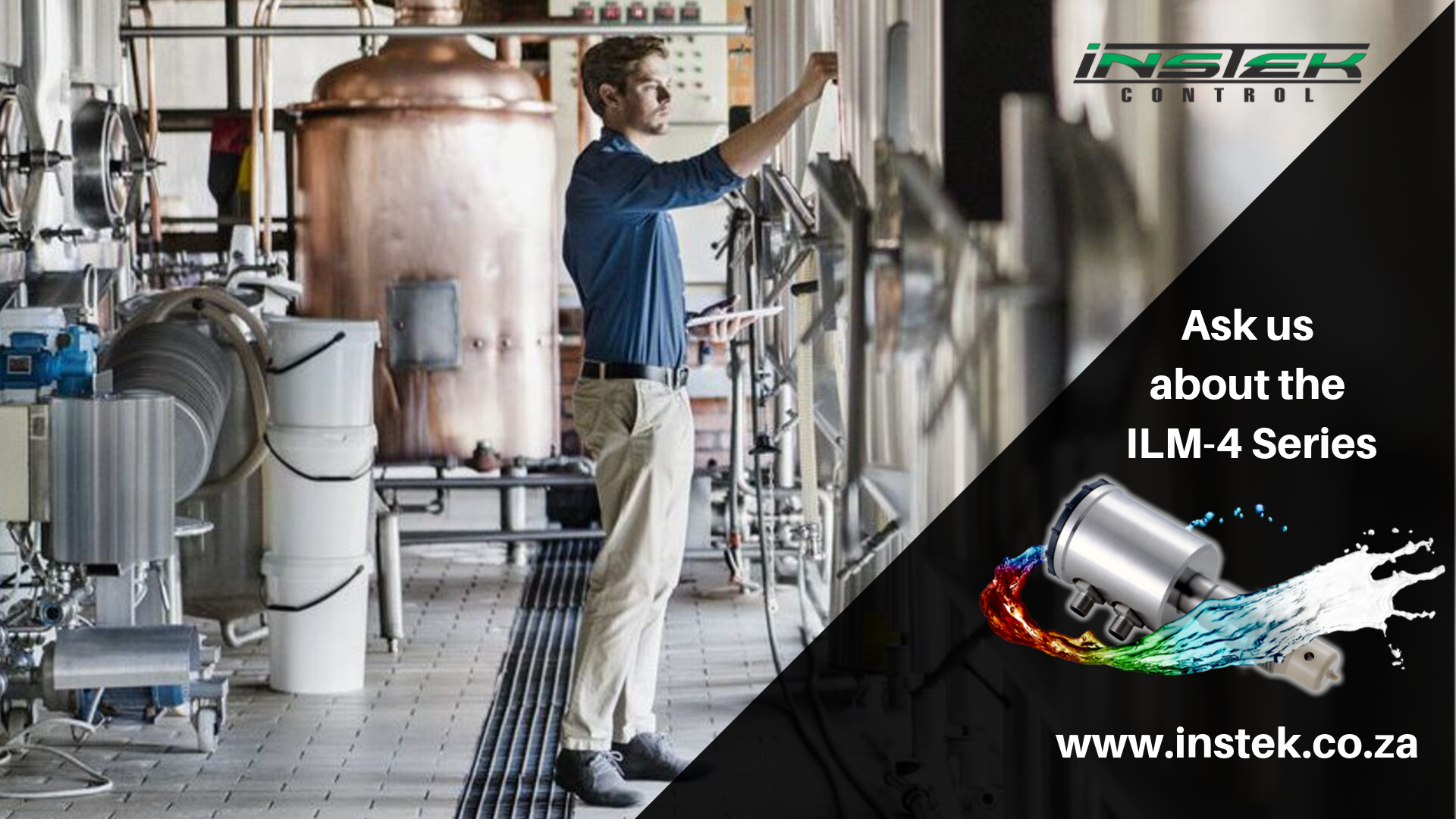