The NEW D3 Differential Pressure and Level Transmitter
The Anderson-Negele D3 Differential Pressure and Level Transmitter is the most complete electronic differential transmitter with best-in-class performance and dual mA output. It uses the proven state-of-the-art temperature compensation technology of L3 and significantly reduces the effects of process and ambient temperature changes.
The diff mA output can be scaled to volumetric values like gallons and lbs. and the second mA output can be used to monitor the top (head) pressure or the bottom (total system) pressure.
While the sensor comes ready for installation right out-of-the-box, the simple graphical interface makes field setup and programming very easy. The D3 transmitter display can be direct mounted to either of the two sensors or can be mounted remotely for easy access.
Range
of applications
-Hydrostatic level measurement in environments with temperature fluctuations
-Differential pressure measurement in tanks up to 110°C (230°F)
-Hydrostatic level, volume and mass measurement in pressure vessels
Application examples
-Hygienic differential pressure and level monitoring for process in breweries, dairies and food and beverage industry
-Pressure drop measurement in diaphragms
Hygienic design/Process Connections
-Use of Negele weld-in sleeve EMZ-352 or build-in system EHG-…/1” results in a hygienic installation situation that is free of gaps and dead space and is easy to sterilize
-Conforming to 3-A Sanitary Standard 74-06 with DIRECTadapt
-CIP-/SIP-cleaning up to 130°C (266 °F) for 60 minutes max
-All material in contact with the product have FDA approval
-Sensors completely made of stainless steel
-Further process connections available through CLEANadapt
Measuring principal of the pressure sensor
In the D3 systems, each sensor uses an internal piezo-electric signal converter and a temperature sensor to measure the pressure and temperature of the capillary fill. The electrical signal of the pressure converter and the resistance of the temperature sensor are measured and converted to a compensated pressure value in the pressure fitting. Both signals are transferred digitally to the head. They are then output in a standardized 4…20mA and HART 7.0 signal for the differential pressure and in a 4…20mA signal for the top or total pressure.
The new D3 is your go-to transmitter for any level applications where pressure and/or vacuum conditions exist.
Contact Instek Control for more information.
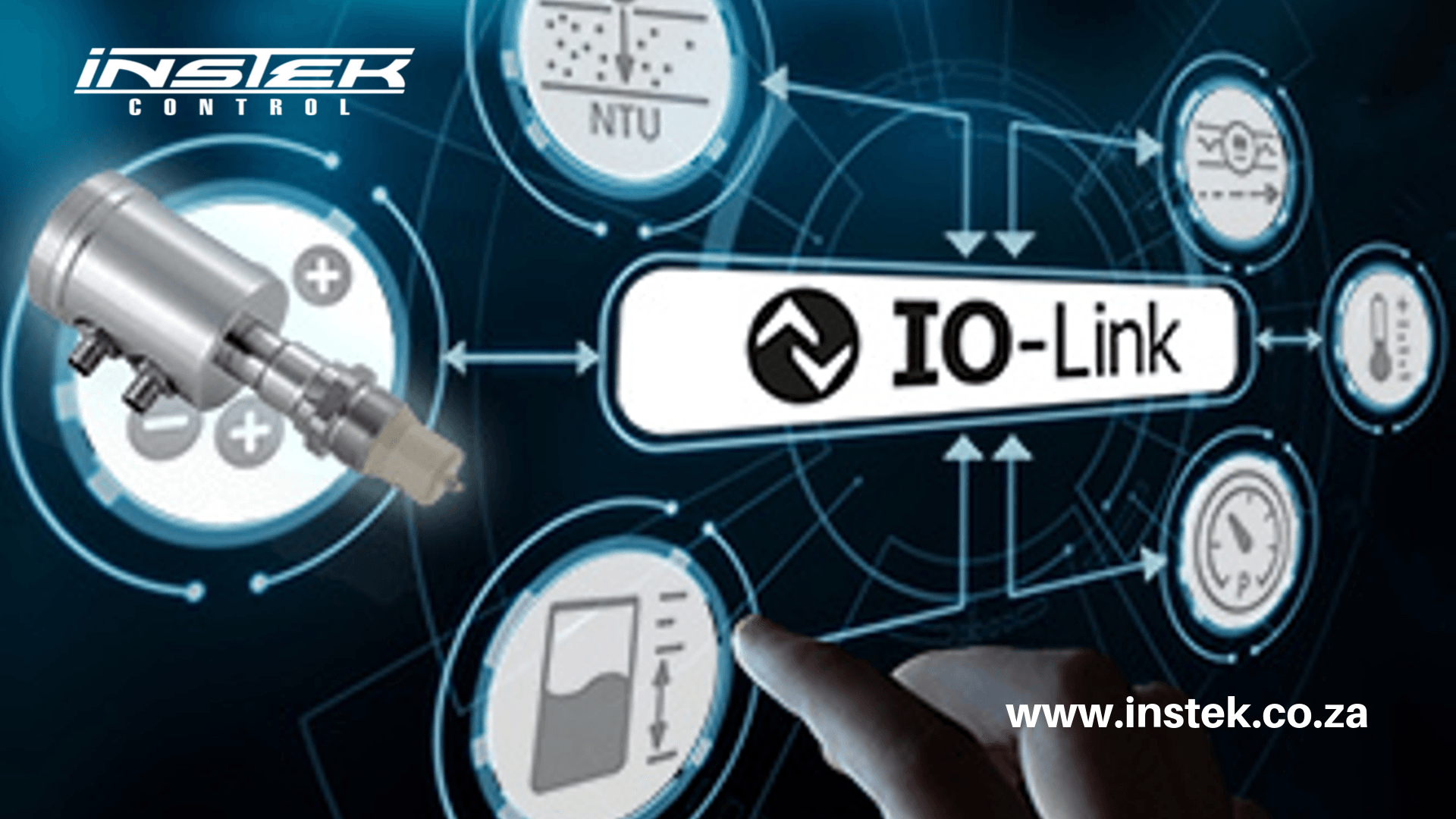
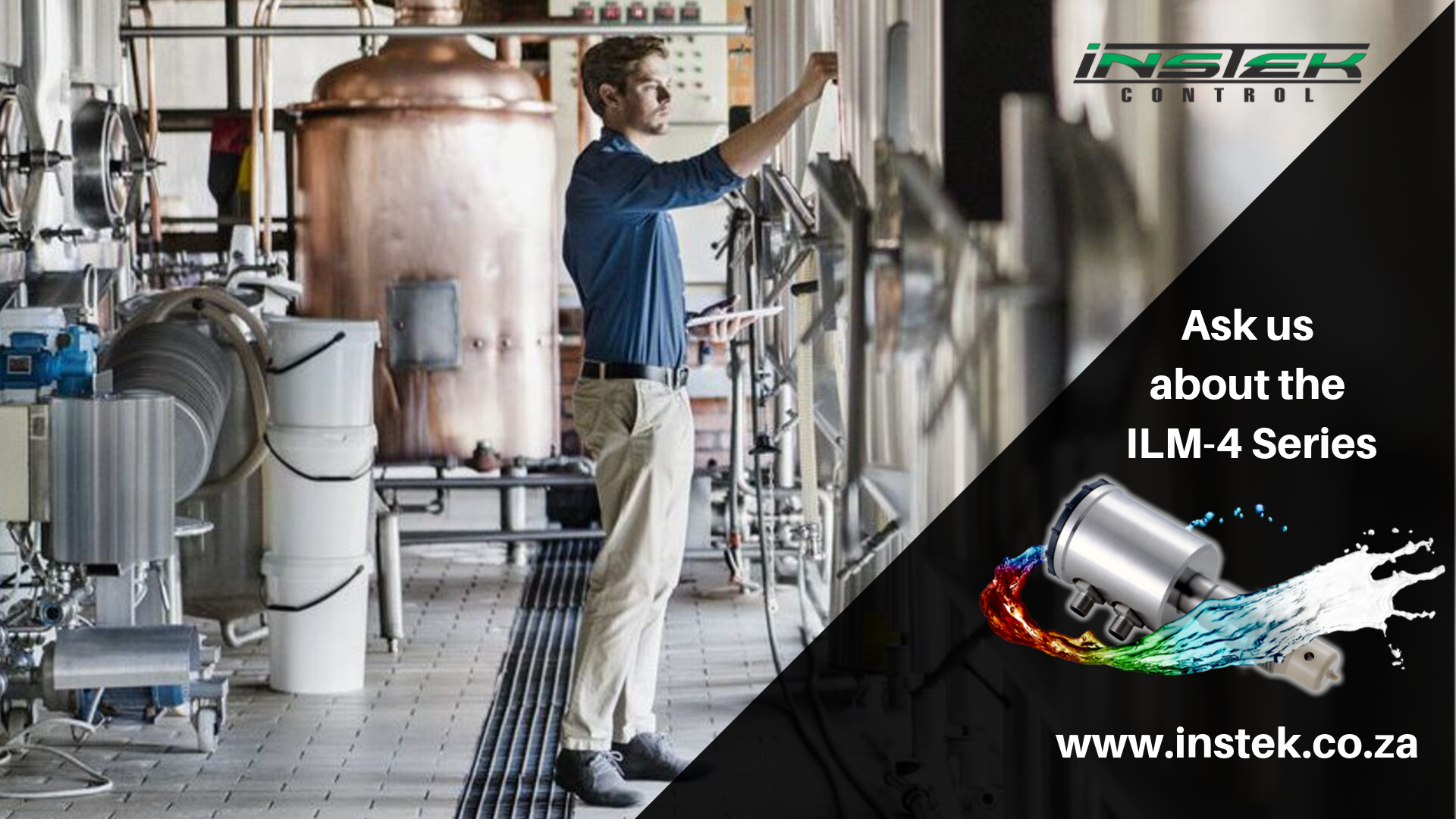