LATEST NEWS
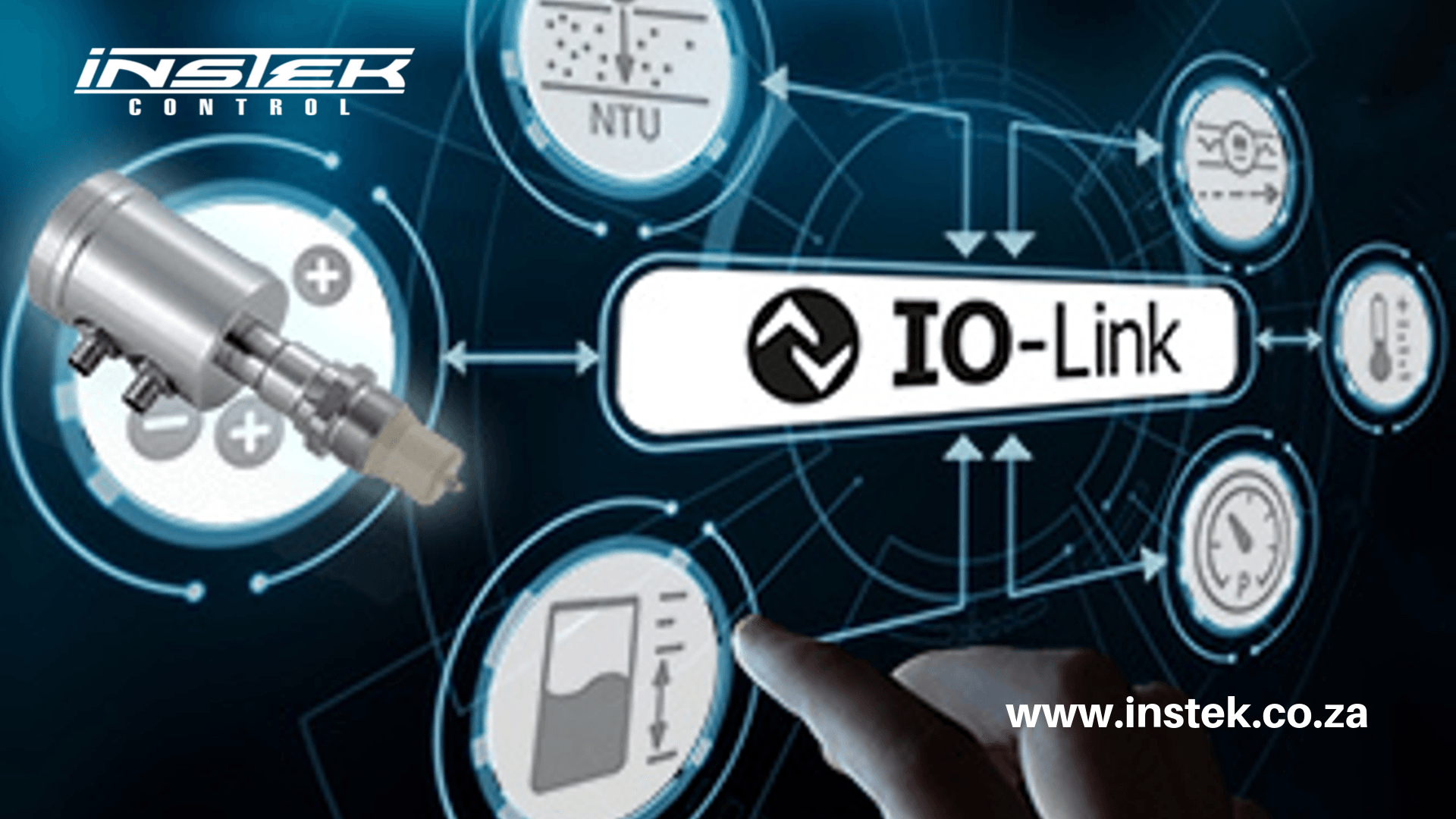
Digitalisation has already found its way into many branches of industry under the keywords "Industry 4.0" or "Internet of Things", and today it is impossible to imagine life without it. INSTEK Control is excited to announce that the new dimension in hygienic measuring technology is digital and analogue, compact or remote and modular.
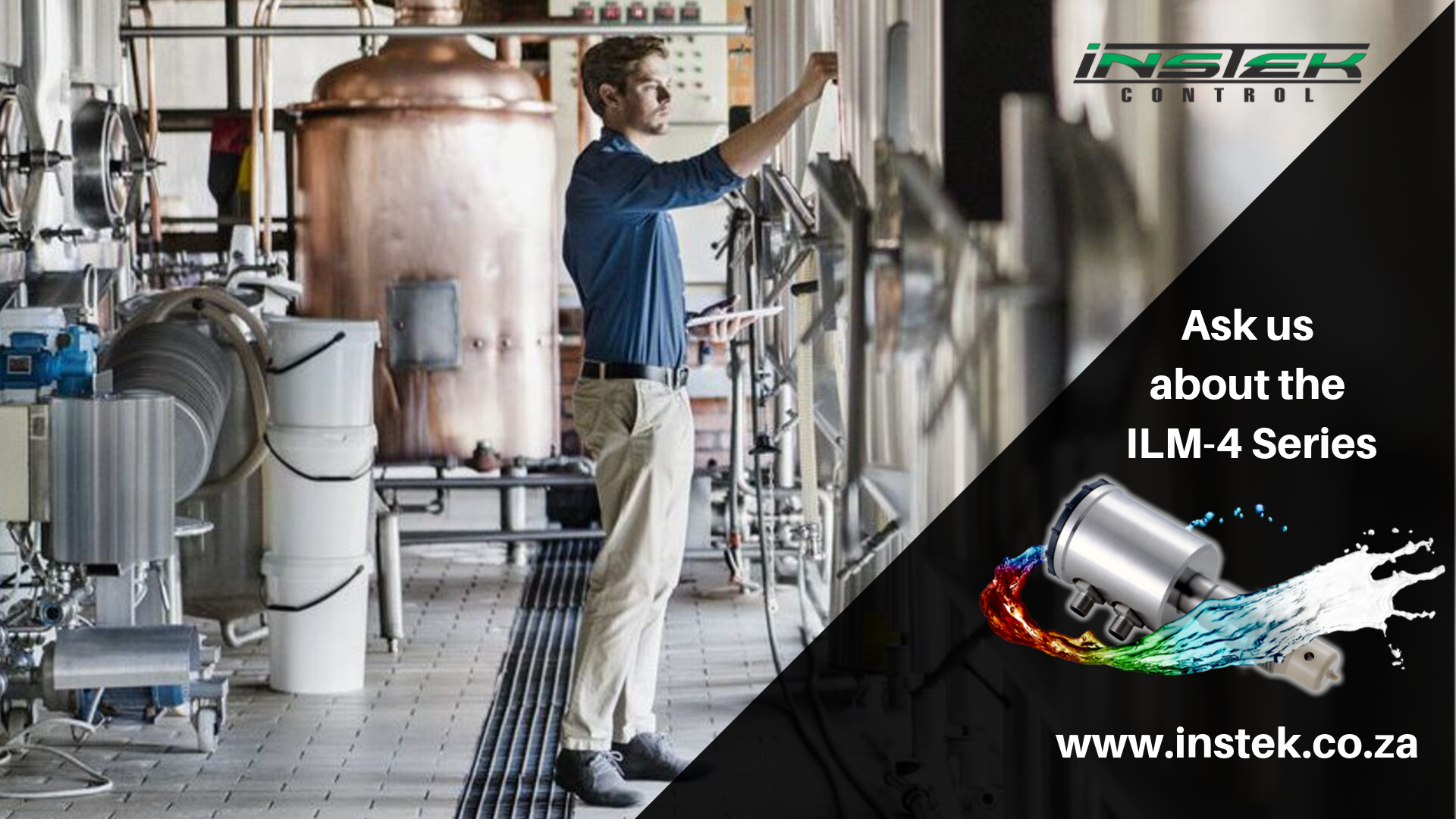
When it comes to a brewery, you clean to prevent the transfer of tastes from one beer to the next, and you clean to help assure your product is safe for human consumption. In the face of increasing supply and demand, brewing plants are compelled to keep the cost of production as low as possible, without sacrificing safety and quality of the end-product.
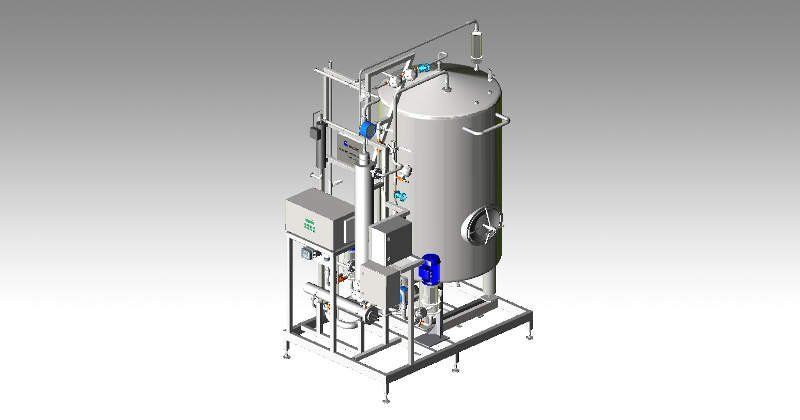
Raw water quality depends greatly on its source. Based on the raw water quality and the specifications for the purified water, Centec select the most appropriate technologies for each client. Usually, multi-stage regimes are necessary for water purification. For water pre-treatment, sand and multi media filters are used to remove suspended material (e. g. silt, clay, organic matter). Such material in water can reduce the effectiveness of downstream components such as ion exchange resins and reverse osmosis membranes. Soluble iron and manganese are found in water that contains no dissolved oxygen. They cause a metallic taste and form deposits in piping systems. The Centec De-Ironizer is designed for iron and manganese removal. If harmful bacteria and microbes are suspected, the water is disinfected by UV, ozone or free chlorine. Activated carbon (AC) filtration removes odours, tastes and oxidizing agents like free chlorine that can lead to chemical attack of membranes elements in subsequent purification steps.
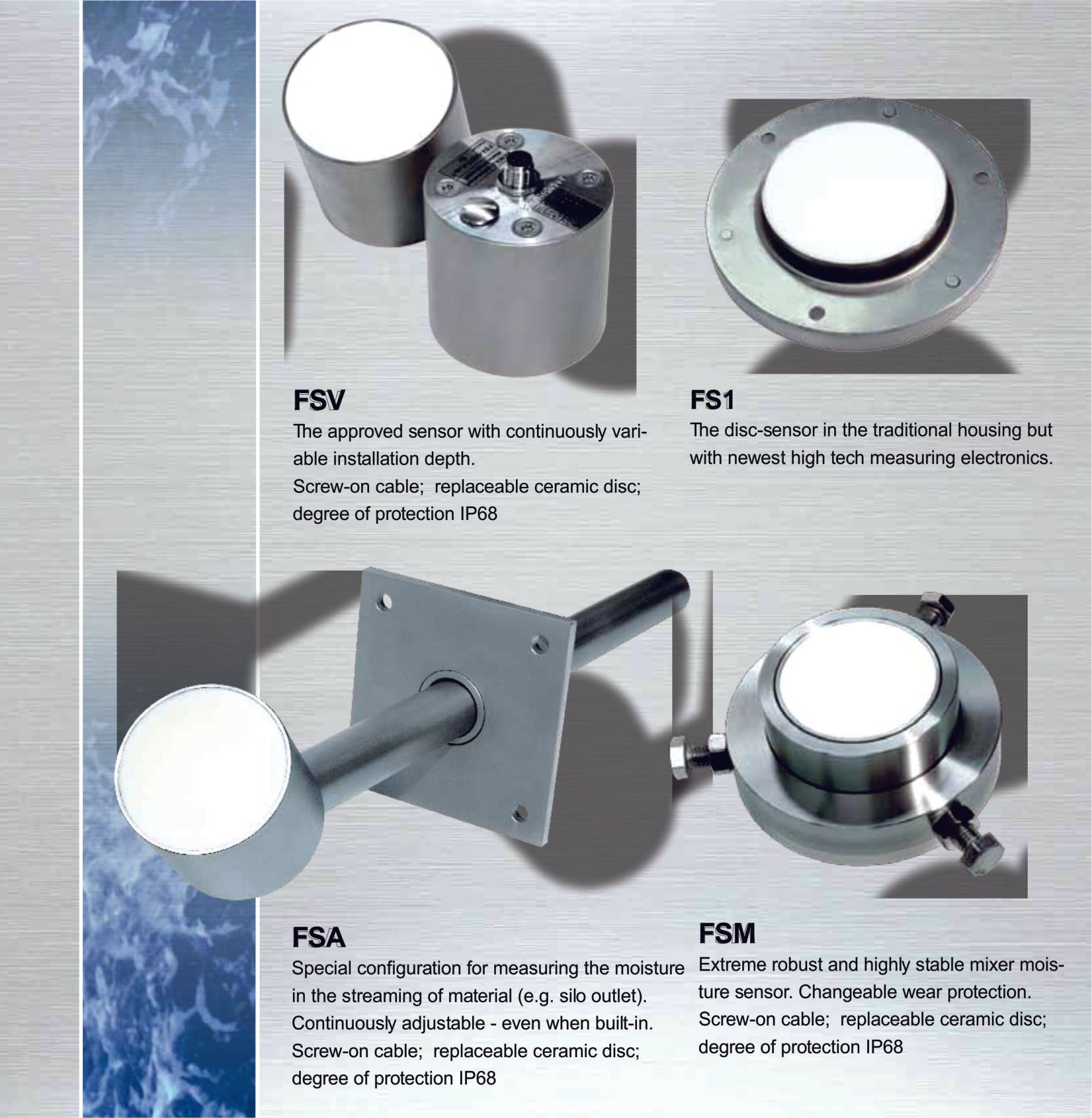
Werne & Thiel moisture measuring sensors always represent the latest technology of our well-proven HPRMethod
(High Frequency Dielectric Polarisation and Field Refraction) and offer unique precision and reliability.
Since decades we are in touch with our customers to be able to always give him an innovative product
perfectly fitting his needs